For the low-density and high strength nature, Aluminum Alloy is ideal for products that need to be lightweight and robust. Extrusion technology is also a key element in the modular automation system. You can use aluminum extrusion in linear slide system.
Whether you are working on a new architectural project or an electronic device manufacturing, choosing the right materials is essential to keep the product lightweight and retain its strengths. Good material selection is always the key.
You will require cost-effective materials that will last longer and keep the desired weight. However, the research and planning you need to do for material collection will easily make you feel drained and irritated.
Here are some critical applications and advantages of using extruded Aluminum for your project that you may consider.
Typical Applications for Extruded Aluminum
Aluminum extrusion is used in all business sectors, including furniture, construction, and automotive industry, because of its’ incomparable mechanical properties. It is a popular choice in:
Furnishing: Aluminum extrusion is used by the furnishing industry and, more broadly, by the architecture sector to create user profiles for furniture, curtains, fixtures, doors, windows, etc.
Electronics: Aluminum extrusion is used in electronics to manufacture elements for photovoltaic plates, inverters, and heat sinks.
Automotive: Aluminum extrusion is useful in the automobile industry to produce parts for radiators, fluid distribution pipes, and other features of air conditioning systems.
Electro-mechanics: Aluminum profiles are used in the electromechanical industry for their electrical conductivity. In reality, it is possible to create extrusions for electrical transformers thanks to Aluminum’s extrusion into alloys with a high purity material.
Lighting: Aluminum profiles are used in this sector to render LEDs, totems, lamps, and also perform the dissipation role of the spare part.
Transport: Aluminum extrusion is predominantly used to prepare different transportation forms, including buses, trains, and vessels. Anodized aluminum profiles should be used to resist degradation in wet conditions or in close contact with water.
Benefits of Using Aluminum
Here are some benefits of using extruded Aluminum for any kind of production:
Weight to Strength Ratio: The strength-to-weight ratio of Aluminum is much greater than that of steel, and its value is just one third the weight of steel. Which has added to the trend of light-weighting in the auto industry.
High-Performance Coatings: Aluminum can be anodized, and to further improve its non-corrosive qualities, high-performance coatings can quickly be added. Even for intense conditions, it may be suitable.
Low Cost: The versatility of Aluminum helps to low tooling costs. Because it is possible to design smaller parts, production is minimized, and assembly is more uncomplicated.
Versatility: Naturally, Aluminum is soft and lightweight. A variety of varying shapes and contours can be carved into the metal.
Non-corroding Properties: Aluminum is corrosion-free. It has an oxide layer that exists naturally, which prevents it from corrosion.
Environment Friendly: The way wood does, Aluminum does not require trees to be cut down. It’s exceptionally recyclable as well.
With all these advantages and possible uses that extruded Aluminum has, you may have concluded that it will be a suitable choice for your project. If you have, you may checkout Robotunit’s extrusion and fastening technology.
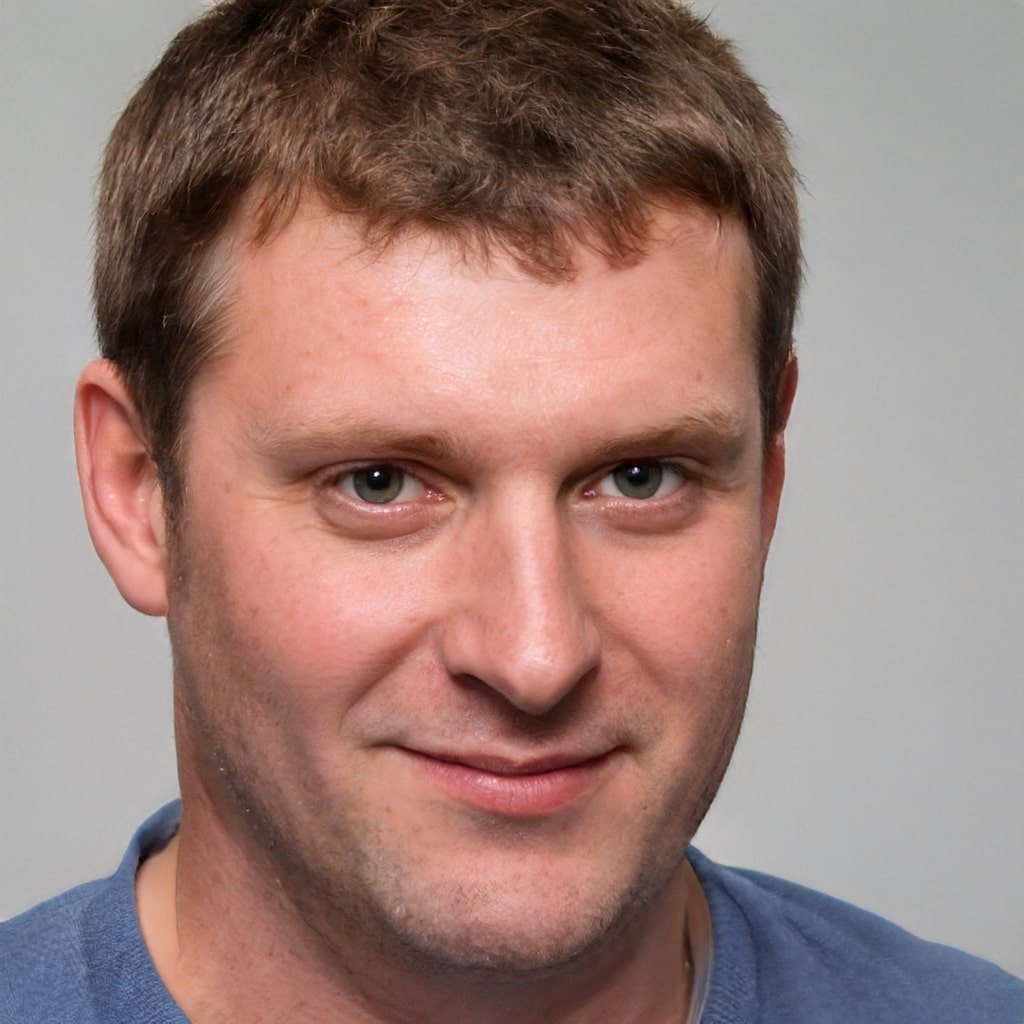